Subidos a una moto o desde la ventanilla de un auto, mirar el paisaje de las cuchillas entrerrianas es parte de la rutina para los trabajadores de Fadel, la empresa avícola, productora de huevos y pollos, de la cual hoy subsisten más de 600 familias oriundas de Concepción del Uruguay, San José, Colón y Pronunciamiento.
No solo se trata de ir desde el hogar hasta el trabajo: la rutina a bordo de los camiones también incluye a los transportistas, quienes vehiculizan la producción entre la planta de incubación, la granja de engorde, la planta frigorífica y subproductos, y la planta de alimentos.
Estas cuatro locaciones, todas en un radio de no más de 45 kilómetros, necesitan del trabajo coordinado y se autoabastecen de manera tal que la empresa mantiene un ritmo de unos 1,2 millones de huevos incubados a la semana, con un resultado final de 140.000 pollos diarios producidos.
“Arrancamos en 2004 con un volumen muy pequeño. Pero nuestro secreto fue que en todos estos años ninguno de los cuatro socios retiramos dividendos de la compañía”, contó Adrián Tornour, presidente de Fadel.
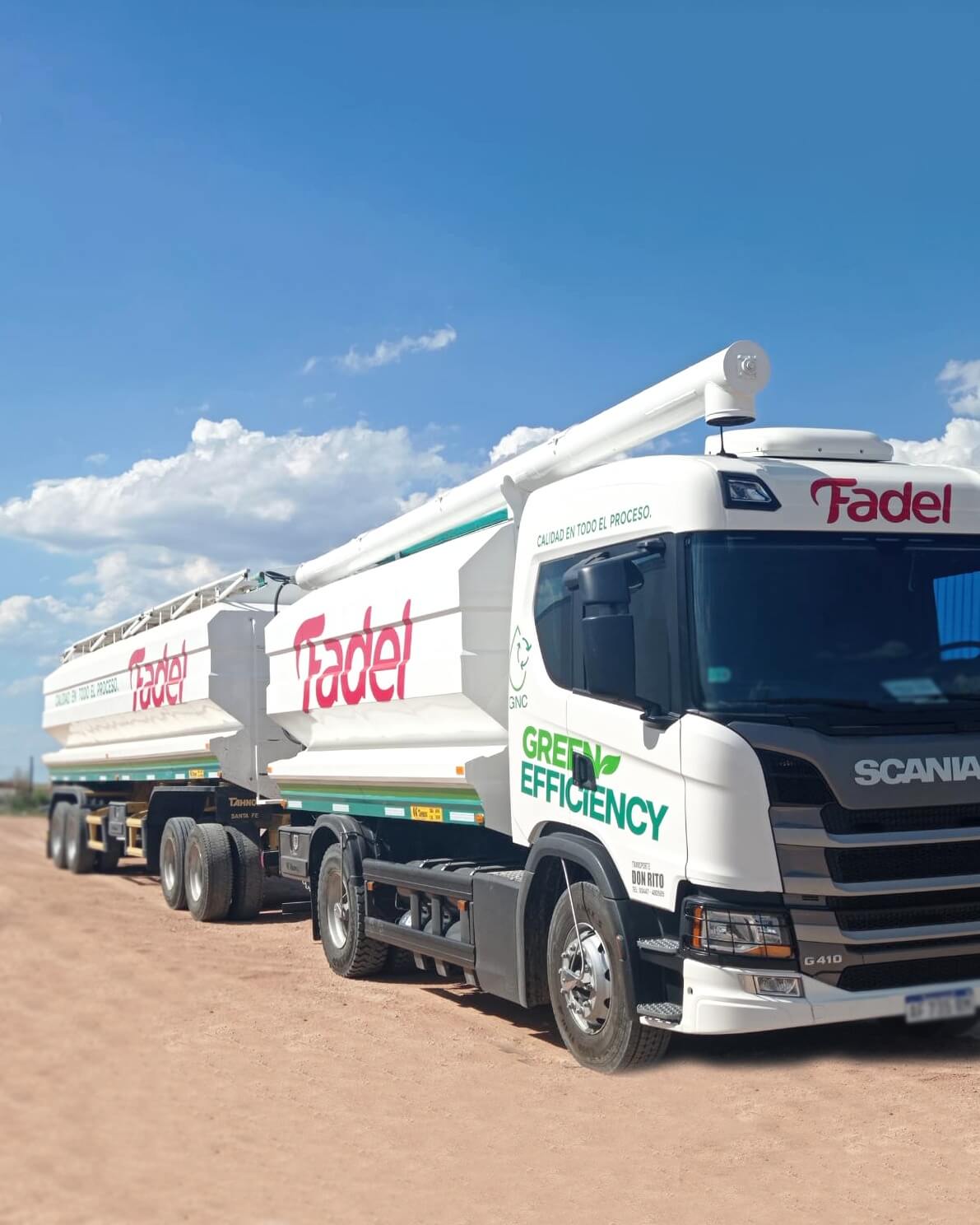
Salir de una crisis y querer aprender cómo evitar caer en la siguiente parece estar en el ADN de los empresarios argentinos. La potencialidad de negocios que ofrece el campo marida también con la resignación de que, después de una crisis, seguramente vendrá otra siguiente. Algunos profesionales toman nota de esto y buscan blindarse, y la historia de Fadel viene por ese lado.
HUEVOS Y POLLOS EN ENTRE RÍOS
Antes de la crisis de 2001, Tornour se dedicaba exclusivamente al mundo del transporte de cargas, pero el estallido lo llevó a salir de ese ámbito y puso su capital en la producción porcina junto a otros socios.
Las inquietudes no terminaron allí. En paralelo se abrió la posibilidad de incursionar en el mundo avícola, y en ese camino, en 2007 sumaron una planta elaboradora de alimento balanceado para acopiar materias primas para los cerdos. Pero en ese mismo año Fadel puso primera en la cría de pollos parrilleros.
En ese inicio se trató de la compra de pollitos bebés y fomentaron el engorde. Luego, invirtieron en la compra de gallinas reproductoras.
“Fuimos escalando en el proceso y hoy por hoy tenemos dos núcleos de recría y postura, de los cuales salen los huevos que van a la planta donde ahora somos nosotros los que hacemos los pollitos bebés”, graficó el presidente de la empresa.
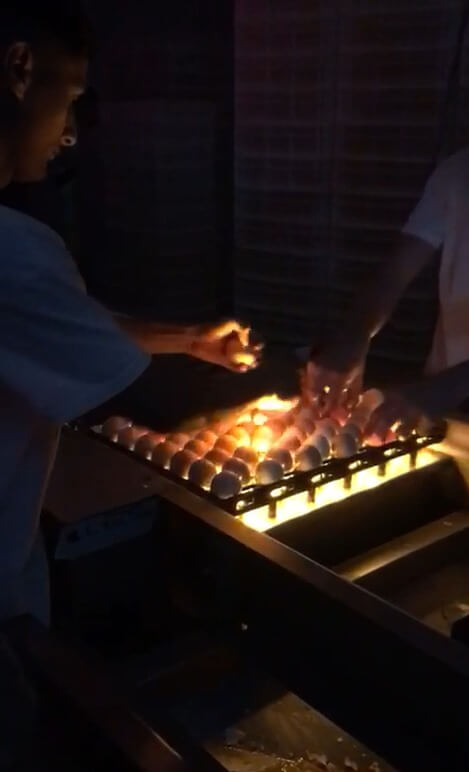
DEL HUEVO A LA GALLINA
Esta semana Infocampo visitó las instalaciones de Fadel, donde Tornour mostró las impresionantes cámaras de incubación en las cuáles llega la producción de esas aves ponedoras. Los huevos son ordenados por peso y tamaño.
Es crucial la detección a oscuras de las anomalías que pueda presentar alguno de ellos: un lente infrarrojo deja en evidencia a los “cascados” de los sanos, y se evita su incubación. Lo que no pueda seguir en el proceso automatizado resulta apartado.
Cada uno de los huevos es vacunado por primera vez mediante una ínfima aguja que penetra la cáscara y aplica la dosis en días en los cuales el animal sin nacer tiene el estómago fuera de su cuerpo. El proceso se hace con el objetivo de que una vez que su formación resulte exitosa el medicamento sea metabolizado.
Con la planta de incubación de San José funcionando al máximo este paso puede hacerse a un ritmo no menor a 55.000 huevos por hora.
“Se hace para evitar que una vez nacido y en la granja el animal contraiga enfermedades”, explicó uno de los jefes de la planta. La misma tiene una capacidad de incubación de 1.300.000 huevos semanales y está gestionada por 30 personas.
Acto seguido, las bandejas ya están listas para entrar en la etapa de incubación, donde Fadel invirtió buena parte de su capital, y también su futuro. Se trata de máquinas de última generación compradas en Brasil en 2017, que fueron puestas en marcha un año después.
MÁS TECNOLOGÍA
Los huevos se meten en la sala de preincubación hasta la hora en la que tienen que entrar a la incubación, a 100 grados farenheit. El paso arranca a unos 20 grados centígrados pero llega a tocar los 37°.
Se trata de un lugar donde el producto entra en un proceso mediante el cual las bandejas en las que está alojado simularán el movimiento de la gallina de manera automática, y rotarán su posición. Pero lo más importante es que garantiza esos miles de nacimientos.
En otra de las salas de incubación visitadas se pudo apreciar que los pollitos recién nacidos que hicieron el rompimiento ya caminan, revueltos en el interior de las bandejas. Se trata de 84 pollitos bebés por cada una.
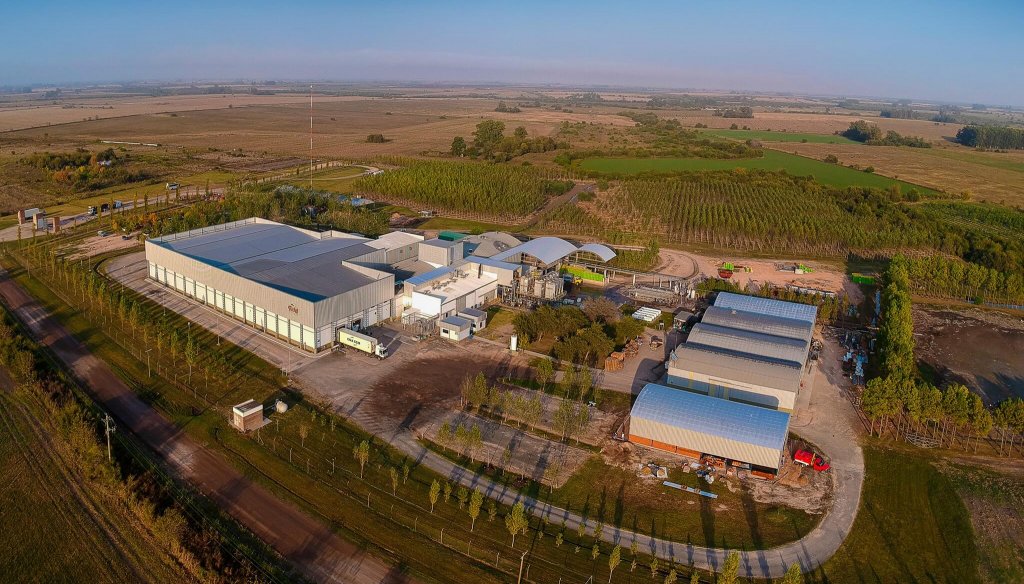
La planta frigorífica de Pronunciamiento emplea a más de 300 personas.
Y si bien el espacio se ve diminuto para sus movimientos, el personal de Fadel revisa la evolución y envía hacia el siguiente proceso a los ya nacidos, mientras que el resto de los huevos sin romperse permanecen allí hasta 21 días en total.
SEPARACIÓN
Entre los empresarios dueños de Fadel el temor pasa por no poder surfear alguna ola que se lleve puesta a la inversión realizada, y que eso se traduzca en suspensiones al personal o reducciones en la planta.
“Queremos hacer las cosas lo más eficientemente posible puertas adentro, pero hay otras que lamentablemente no dependen de nosotros y por eso tratamos de acomodarnos”, contó Tornour.
Una de esas situaciones se vivió este año con el estallido de la gripe aviar en el país. Si bien la empresa “zafó” de tener que sacrificar aves de sus galpones, el cierre de mercados exportadores como Arabia Saudita, la Unión Europea, China y Chile se hizo sentir.
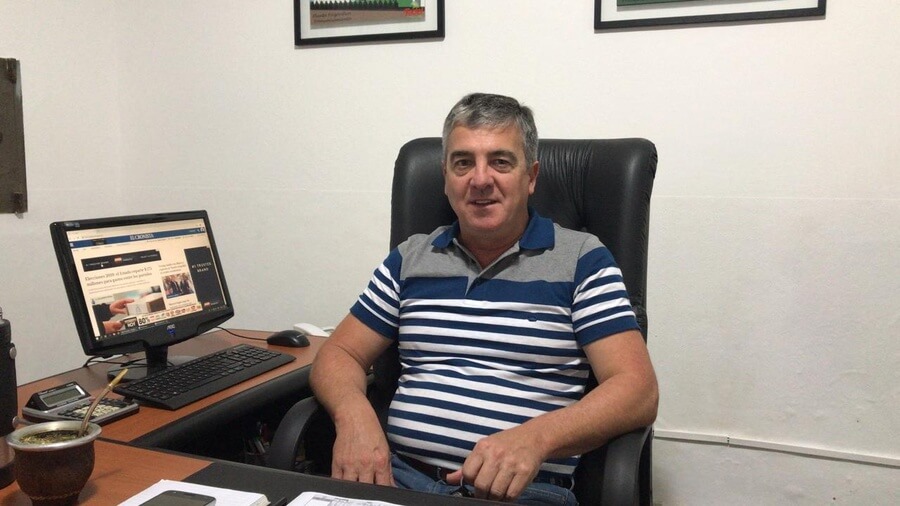
Para Tornour, el secreto de la empresa fue el compromiso de los socios.
“China por su tamaño sería crucial volver a incorporarlo, pero Brasil aprovechó y se metió. Y venderle a Chile también, porque si bien representa lógicamente muchísimo menos volumen, los chilenos son consumidores que aprecian mucho al pollo argentino y lo resolvemos con el envío de uno o varios camiones, sin acudir a un buque”, expresó el dueño de la firma.
Por eso, una de las maneras de hacer más eficiente el proceso de agregado de valor es el de generar una harina con lo descartado durante el proceso de producción de pollos por unidad o en el prometedor segmento de los trozados. Con dicha harina, hoy, se alimenta a un corral de bovinos que posee la empresa y en el mismo se realiza un engorde a campo.
“Nosotros estamos ‘cortando’ el 70% de los pollos que producimos, porque el mercado del trozado es muy alentador. La de pollo es una carne con proteína animal que se consigue en góndola más barata que la carne bovina, y tiene gran terneza”, comparó Tornour.
Algunas de las variantes que se analizan pasan por meterse de lleno en el segmento del pollo frito o los precocidos. “No veo que la manera tradicional de comer pollo pueda crecer mucho”, lamentó.
UN PROYECTO EN CONSTRUCCIÓN
En tanto, a media hora de viaje en camioneta, se levanta la construcción de la “Granja Alcides”, unos 12 galpones de casi dos cuadras de largo por 16 metros de ancho. Uno de los mismos ya está terminado, pero la mayoría del predio aún está vacío y sin los 43.200 animales que pueden entrar en cada galpón, con el propósito de ganar peso y kilos de carne.
El galpón que está listo ya cuenta con el sistema de alimentación e hidratación de las aves, a base de maíz y derivados de la soja. Otros tres están en pleno armado y el resto por ahora en la planificación. Se espera que el sitio ubicado entre Colonia Hocker y Pueblo Cazes albergue a casi 520.000 aves en total.
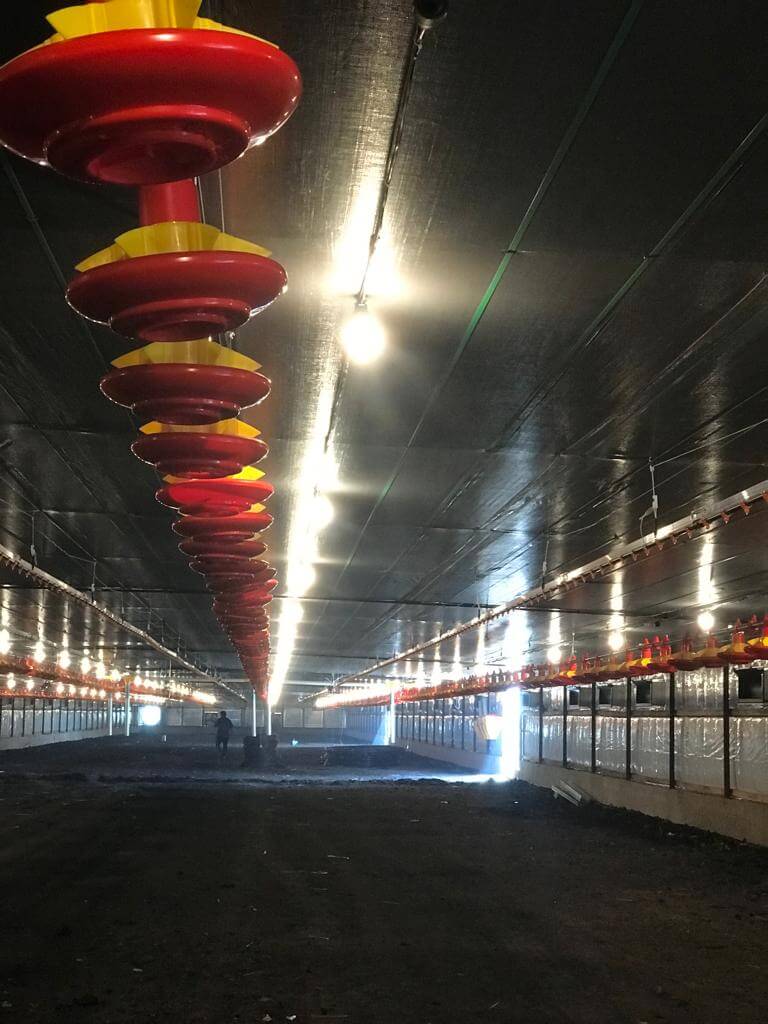
Según expresan los empleados de Fadel que dirigen la construcción, el retorno de lo invertido en la granja muestra lo fructífero del mundo avícola en estas escalas de producción. Uno de los especialistas presentes en el lugar señaló entre 4 y 5 años los tiempos para recuperar lo invertido.
El lugar contará con tecnología black-out para evitar que se vea el sol y acelerar los tiempos de crecimiento, pisos renovables con una cama de aserrín, combustible para la calefacción a base de chips de madera y una potencia eléctrica de 400 kilowatios.
¿La idea? Desde Granja Alcides se apuntalará la demanda de la mega planta frigorífica y de subproductos ubicada en Pronunciamiento, a más de 40 kilómetros de allí a través de un camino de ripio.
AUTOMATIZACIÓN
Uno de los puntos que más entusiasma en Fadel está vinculado al clásico código QR que acompaña el rotulado de los alimentos en la actualidad. En la empresa se definen como precursores en la materia.
Según explican, de darse algún problema con alguna partida una vez llegada a destino, el fabricante tiene 48 horas para demostrar la trazabilidad del envío.
“Europa está trabajando en el seguimiento a la huella ambiental de las producciones, y seguramente en algún momento nos van a demandar información. Pero nosotros algún pasito ya hicimos porque hace un par de años que con cualquier teléfono celular en Fadel podemos demostrar la trazabilidad desde la reproductora hasta la planta de faena. Esto lo presentamos en 2019 en Alemania y realmente afuera lo valoraron mucho, más que acá”, aseguró el presidente Tornour.
En dicha planta el clima es de refrigeración total y ya no se ven huevos ni pollitos bebés. Por una cinta y a buena velocidad circulan pollos recién faenados, sin plumas, y colgados en ganchos típicos de cualquier línea fabril.
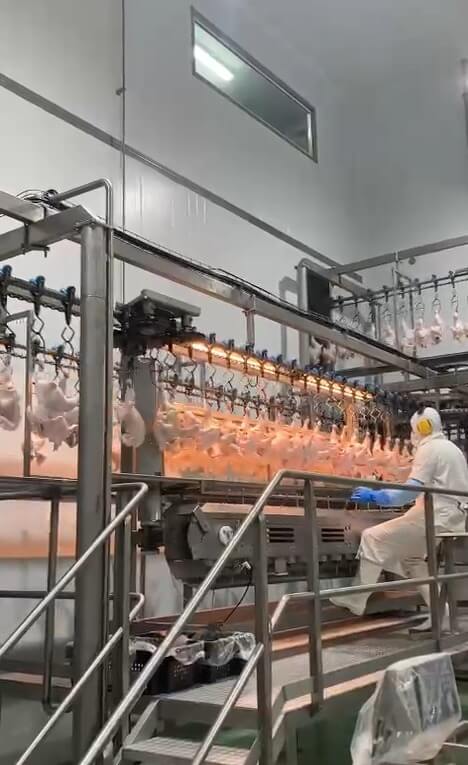
Uno de los primeros puestos que interviene en el movimiento es el de un operario que rota cada dos horas, cuya única función es la de ver pasar miles de pollos al día y detectar defectos en la piel.
Los que están en mejores condiciones se separan, se empaquetan de acuerdo al tamaño y peso y se venden como pollos enteros, uno de los mercados más pequeños que se abastecen. El resto, la inmensa mayoría, pasará al troceo.
Este paso también es completamente automático y no intervienen operarios. El presidente de Fadel sugiere que de este modo “no existen problemas de tendinitis ni lastimaduras con el cuchillo”. Apenas unos pocos empleados ultiman algunas piezas que requieren de alguna pasada manual que las deje listas para congelarlas en otro sitio de la planta, y en cuestión de segundos.
Aquí el frío ya aprieta y los dedos se entumecen como para portar teléfonos o algún cuaderno anotador. Las máquinas están programadas para clasificar los productos de acuerdo a su empaque final: pata muslo con y sin hueso, cuartos traseros, muslitos y supremas, alitas, trozos con o sin piel, etc. El ruido de las piezas congeladas cayendo sobre los metales desde una altura de un primer piso es constante y por momentos ensordecedor.
A lo lejos, una de las bolsas de empaque parece distinta a las demás. “Esa máquina está armando bolsas de alitas que saldrán para Vietnam”, explicó un operario que seguía a la distancia esa operación.
“El pollo entero termina siendo un commoditie y por eso nos volcamos de lleno a los trozados, porque la comercialización es más estable”, aseguró el titular de la empresa.